Week 27 : 2/20/2023 - 2/27/2023
- Group Progress
- Feb 26, 2023
- 2 min read
This week the group started with the first full mock test of the system by integrating the solar panel, PWM charge controller, and vent visors to the test vehicle and diagnosing any issues. The vent visor assemblies were placed on each of the four windows with wires routed through the doors and into the electrical box which housed the control circuitry and PWM charge controlled. Following the setup required, the battery was hooked up to the PWM charge controller, followed by the solar panel and then the load output was wired to the Buck-Boost converter of the control circuitry. For initial testing, the Pico was powered off of a laptop that would display information regarding each window's current temperature, the voltage of the battery as read by the ADC, the number of active fans based on the battery voltage, whether any windows were up, and the current cooling mode (airflow direction) based on temperature differences between the window.

Notable issues included a rather large difference between the expected voltage at the ADC and the determined voltage displayed by the code, up to nearly 100mV. As well, the IR sensors had an exceptionally weak signal as seen at the ADC of the Pico, ranging between 30mV and 40mV when we expect upwards of 1V to 2V when the windows are down.
The battery voltage issue was later corrected by the implementation of a formula developed by Ian which would correct for the deviations within the code itself by correcting for the somewhat bouncy ADC. Following its introduction, the deviation between the expected value and the read value was only 10mV to 20mV on average. The IR sensor issues would be troubleshot throughout the week by Daniel.

An initial concept design was drawn by Daniel and given to Ian to implement in Fusion 360 to create a printable 3D model for testing. A prototype was printed and brought over to confirm airflow capabilities and testing sizing constraints. For the front window, there are no apparent issues related to size as shown in the video below.
On the back window however, there is a potential issue. While there is clearance between the nozzle and window this clearance is minimal (only 2mm approximately) and there is a likelihood that excess vibration from the vehicle while driving would cause the nozzles of the rear windows to tap against the windows potentially damaging them and scratching the window.

Initial airflow appears to be adequate but there is room for improvement. There may be losses associated with the non-airtight seal that we will have when they are epoxied to the intake fans. As well, the airflow channel is rather constrictive and may need lengthened/widened on the interior to allow better airflow from the outlet of the intake fans. Modifications will be made by Ian and further testing will be done in order to optimize the airflow from the intake fans.
Lastly, financial information for the IEEE was gathered by the group with a bill of material and set of receipts gathered for reimbursement by the Region 3 Treasurer. Information for filling out a report in SAP Concur was requested from Joe Juisai for reimbursement.
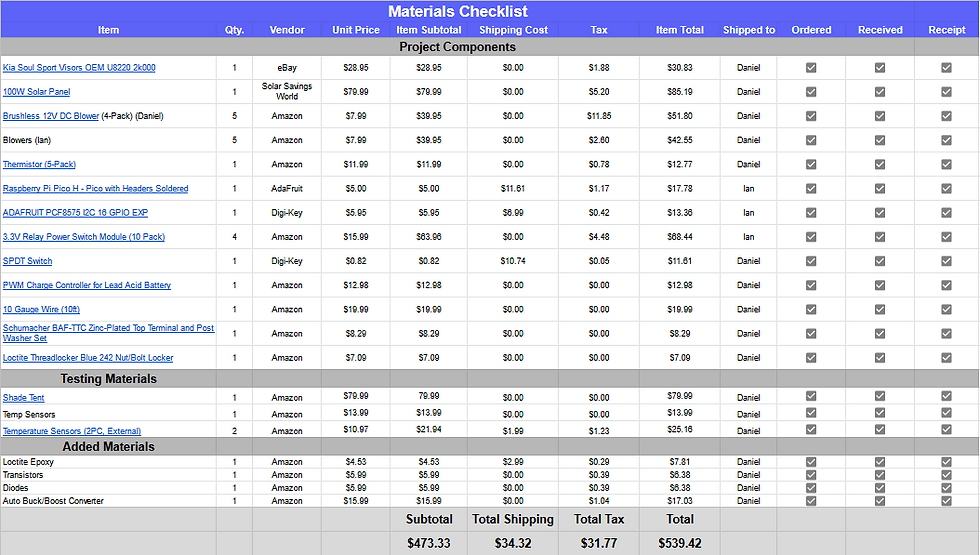
Comments