Week 29: 3/6/2023 - 3/13/2023
- Group Progress
- Mar 14, 2023
- 3 min read
This week, the group aimed to get the full system attached to the car and functioning properly so that they could begin full-system temperature testing the following week.
Preparing and Mounting the Vent-Visor Fan Assemblies
Using lots of zip ties, the group wrangled the fan cables into something manageable. Zip-tie surface mounts were attached to the vent visors using nuts and bolts, and these were used to zip-tie the cables in place.

Until this point, the vent visors had been quite resilient to drilling and mounting. Fastening the final screws for cable mounting put too much stress on the visors, however, and resulted in some terrifying cracks. Pictured below are two of the most gruesome examples.
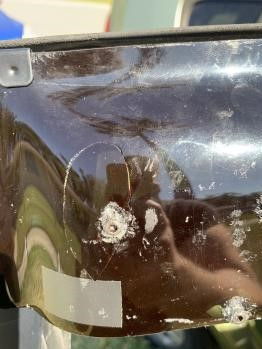

In an attempt to amend these breaks, the group applied hefty amounts of Flex-Glue to them. In some areas, some electrical tape and/or epoxy were also used.





During the mounting process, the ground wire for one of the fans became disconnected. A quick resolder and wrap was all it needed.
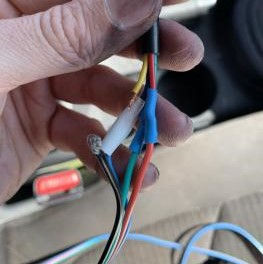
Later, Duncan Kurtz came with a special delivery of six freshly printed nozzles for the rear intake fans. The group applied epoxy to them and affixed them to their fans.
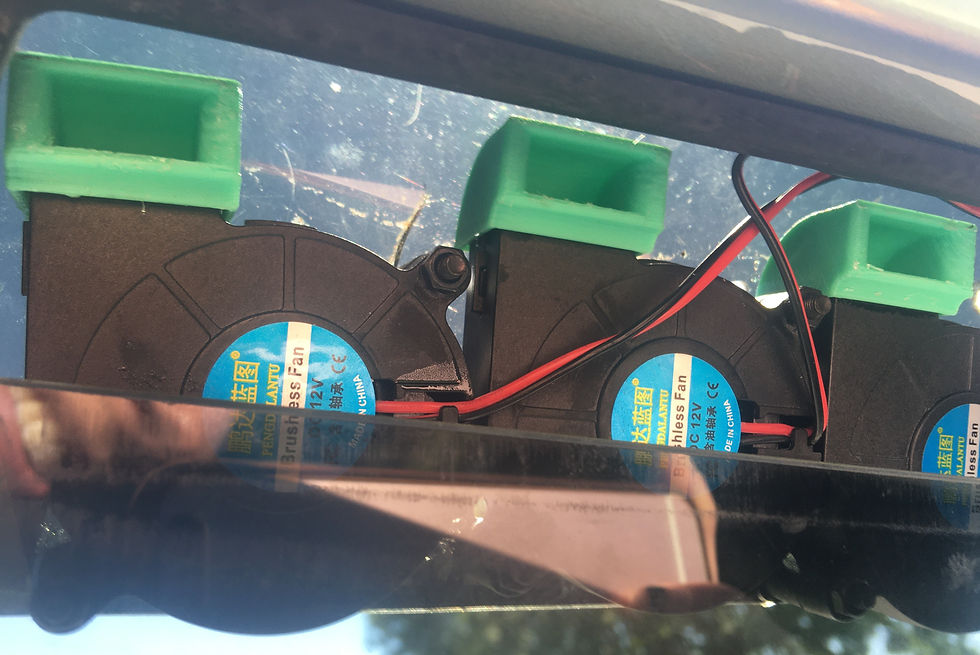
Ultrasonic Proximity Sensor Testing and Troubleshooting
Once the vent visors were patched up and adhered to the testing vehicle, the group set about testing the ultrasonic proximity sensors. Running the program that Ian wrote this week, the sensors immediately presented some issues. The distance value came back lower than it did in the lab and the sensors weren't as sensitive to objects in close proximity. Also, one of the sensors seemed to be far less sensitive than the others, making it impossible to properly set the switching threshold.
First, the group used an oscilloscope to verify that the correct signals were being sent and received by each sensor. Once this was verified, the group began modifying the program to adjust the sensitivity of the sensors. A variety of pulse frequencies and repetitions were tested to no avail. The group decided that a rewriting of the program could prove beneficial at this stage.
Going by the HC-SR04 datasheet [1], the sensor can be triggered by a 10us or greater pulse. At the falling edge of this pulse, the transmitter will emit an 8-cycle sonic burst at 40 kHz. The Echo Pulse lever signal output which follows is proportional to the proximity of the sensor to the object it is directed towards.


The flowchart to the left shows how the new program works. After setting the distance variable to 0, the Pico sends a 10us pulse to the HC-SR04. Immediately after, the Pico reads the ADC connected to the HC-SR04 Echo pin every microsecond for a specified number of repetitions. Once the specified number of reps has occurred, the program returns the average distance value.
Testing the program in the vehicle, the sensors were far more sensitive and consistent, but one sensor had reduced sensitivity. The group adjusted the number of repetitions until the sensitivity of all the sensors was great enough. 150 repetitions worked very well, and a new switching threshold was set at a distance of 2500000.
The group tested the functionality of the proximity sensors according to the test procedures laid out by Daniel: by rolling down all of the windows and then rolling them up one at a time. Per the engineering requirements, power should be disconnected from the fans if any of the windows are rolled up too high for airflow. The green LED should also be on when the windows are down and off if they are up.
The results of the test indicate that the proximity sensor circuit and control are functioning exactly as intended. When any of the windows are rolled up too high for airflow, the fans and the green LED shut off. When all windows are low enough, the fans and green LED automatically turn back on. This constitutes a pass for the engineering requirement concerning window sensors.
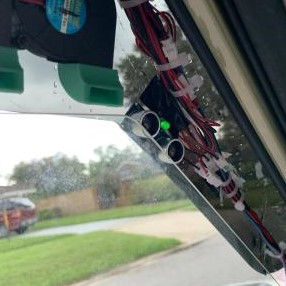

Summary
This week the group prepared the vent-visor fan assemblies and mounted them to the test vehicle. A number of things broke, but the group was able to amend all of the breaks. Some spray-on adhesive will be applied next week to ensure that the structural integrity of the vent visors is not compromised while driving. The new rear window intake nozzles were affixed to their respective fans. The group also ran testing and troubleshooting on the ultrasonic proximity sensors. Once the sensors were fixed, the group verified their operation within the system and determined that the engineering requirement has been met. The group also began writing the report, starting with chapters 1 and 2.
Comments